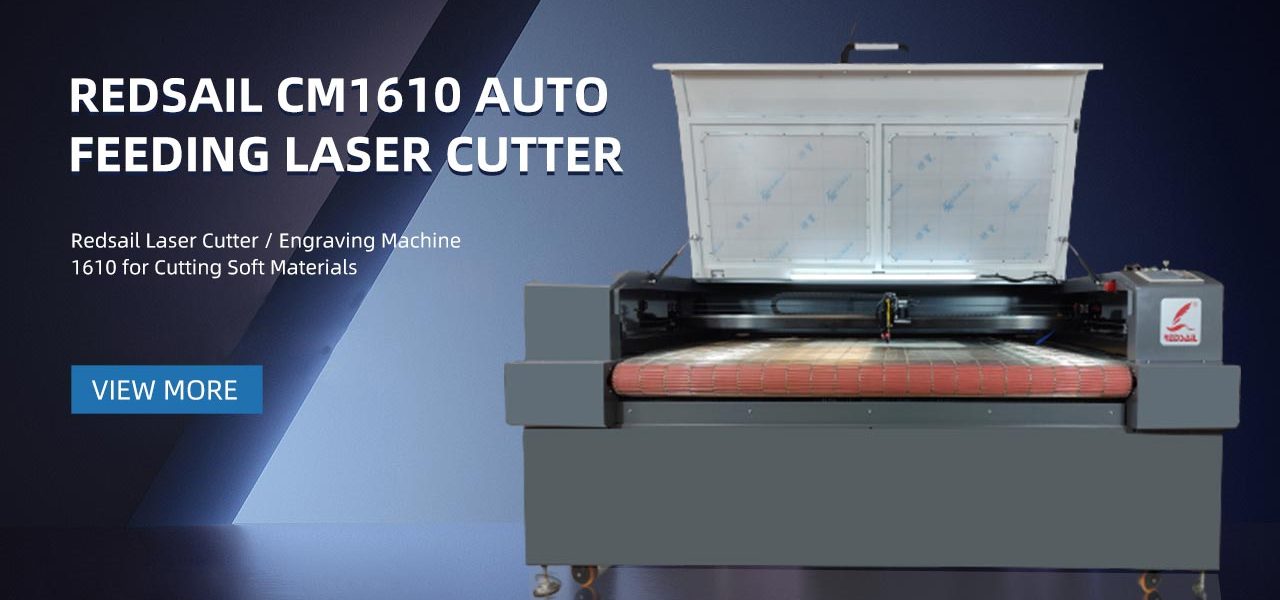
RF CO2 laser cutting is a cutting-edge technology that has revolutionized the manufacturing industry. With its ability to cut through a variety of materials with precision and speed, it has become a preferred method for many manufacturers. The use of RF CO2 laser cutting has led to an increase in efficiency, reduced lead times, and improved product quality. In this article, we will explore the efficiency of RF CO2 laser cutting and how it has helped streamline the manufacturing process.
Improved Precision
RF CO2 laser cutting offers unparalleled precision, allowing manufacturers to cut intricate and complex designs with ease. This level of precision ensures that the final product meets the highest quality standards, reducing the need for rework and minimizing waste.
Reduced Lead Times
With its high cutting speed, RF CO2 laser cutting has significantly reduced lead times in the manufacturing process. This allows manufacturers to meet tight deadlines and deliver products to their customers more quickly, ultimately improving customer satisfaction.
Enhanced Product Quality
The precision and speed of RF CO2 laser cutting result in products with consistent quality. This ensures that each piece is identical, meeting precise specifications and customer requirements. The improved product quality has minimized defects and rejections, ultimately saving time and resources.
Cost Savings
RF CO2 laser cutting has also led to cost savings for manufacturers. The reduced lead times and improved product quality have resulted in higher productivity and lower production costs. Additionally, the precision of the cuts has minimized material waste, further reducing costs for manufacturers.
FAQs
What materials can RF CO2 laser cutting process?
RF CO2 laser cutting can process a wide range of materials, including but not limited to metal, plastic, wood, rubber, and ceramics.
What are the typical applications of RF CO2 laser cutting?
RF CO2 laser cutting is commonly used in industries such as automotive, aerospace, electronics, medical devices, and signage, among others.
What is the maximum thickness that RF CO2 laser cutting can handle?
The maximum thickness that RF CO2 laser cutting can handle varies depending on the material being cut. However, it is capable of cutting thicker materials compared to other cutting methods.
In conclusion, the efficiency of RF CO2 laser cutting has streamlined the manufacturing process for many industries. Its precision, speed, and cost savings have made it a preferred method for manufacturers looking to improve their productivity and product quality. As technology continues to advance, RF CO2 laser cutting will undoubtedly play a crucial role in the future of manufacturing.