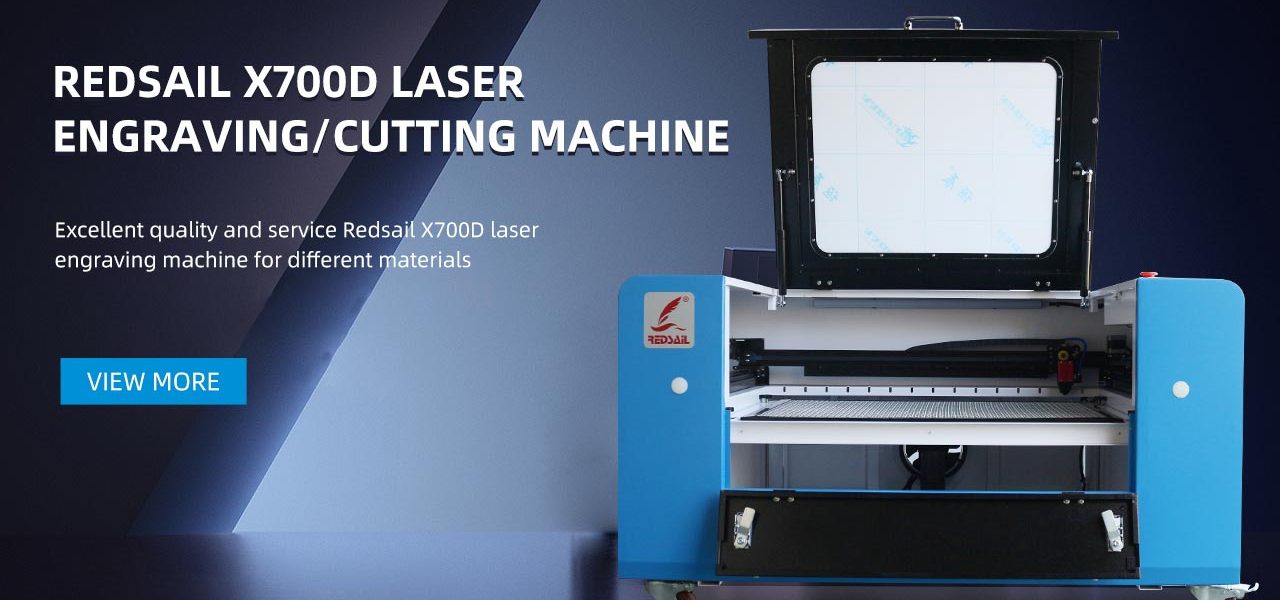
When it comes to rubber manufacturing, precision and efficiency are key. That’s why many manufacturers are turning to CO2 laser cutting technology to meet their production needs. CO2 laser cutting offers a wide range of benefits that make it an ideal choice for cutting and engraving rubber materials. In this article, we’ll explore the advantages of using CO2 laser cutting technology for rubber manufacturing.
Benefits of CO2 Laser Cutting for Rubber Manufacturing
Precision Cutting
CO2 laser cutting technology provides unparalleled precision when cutting rubber materials. The high-powered laser beam can create intricate designs and cut through rubber with high accuracy, ensuring that the final product meets the exact specifications required by manufacturers.
Efficiency
CO2 laser cutting is a highly efficient process that allows for rapid production of rubber components. The laser technology can cut through rubber quickly and with minimal waste, resulting in increased productivity and cost savings for manufacturers.
Versatility
CO2 laser cutting technology can be used to cut and engrave a wide range of rubber materials, including silicone, neoprene, and natural rubber. This versatility makes it an ideal choice for manufacturers who work with a variety of rubber products.
Minimal Tooling Required
Unlike traditional cutting methods, CO2 laser cutting does not require complex tooling or setup. This means that manufacturers can quickly and easily change designs and production runs without the need for extensive retooling, saving time and reducing production downtime.
FAQs about CO2 Laser Cutting for Rubber Manufacturing
Is CO2 laser cutting safe for rubber materials?
Yes, CO2 laser cutting technology is safe for rubber materials. The laser beam does not cause any damage to the rubber and leaves a clean, precise cut.
Can CO2 laser cutting be used for intricate designs?
Yes, CO2 laser cutting is capable of creating intricate designs with high precision. This makes it an ideal choice for manufacturing rubber components with complex shapes and patterns.
What are the cost benefits of using CO2 laser cutting for rubber manufacturing?
CO2 laser cutting can result in cost savings for manufacturers due to its efficiency and minimal waste. The rapid production and precise cutting capabilities of CO2 laser technology reduce production time and material waste, leading to overall cost savings in the manufacturing process.
How does CO2 laser cutting compare to other cutting methods for rubber materials?
CO2 laser cutting offers advantages over traditional cutting methods such as die cutting or water jet cutting. It provides greater precision, efficiency, and versatility, making it a preferred choice for rubber manufacturing.
In conclusion, CO2 laser cutting technology offers a range of benefits for rubber manufacturing, including precision cutting, efficiency, versatility, and cost savings. Manufacturers can rely on CO2 laser cutting to meet their production needs and create high-quality rubber components for various applications.