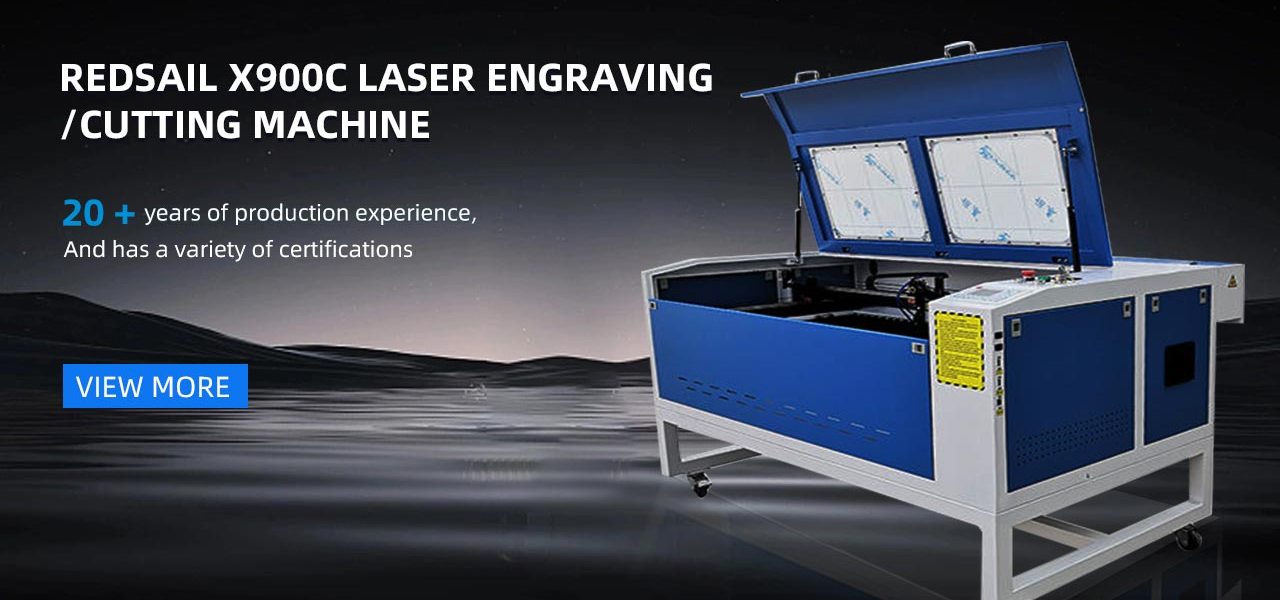
Optimizing CO2 Laser Cut Quality with Troubleshooting
In recent years, CO2 laser cutting technology has become a popular choice for a wide range of manufacturing industries due to its precision, speed, and versatility. However, achieving the best possible cut quality with a CO2 laser cutter requires careful optimization and troubleshooting to overcome any issues that may arise during the process. In this article, we will explore some key tips for optimizing CO2 laser cut quality and common troubleshooting techniques to ensure the best results.
Understanding the Basics of CO2 Laser Cutting
Before diving into the optimization and troubleshooting tips, it’s important to have a basic understanding of how CO2 laser cutting works. A CO2 laser cutter uses a high-powered laser to melt, burn, or vaporize material with extreme precision. The laser beam is guided by mirrors and focused through a lens to create a fine, precise cut. The material is typically held in place by a cutting table or fixture, and the laser moves across the material according to a programmed pattern.
Optimizing CO2 Laser Cut Quality
To achieve the best possible cut quality with a CO2 laser cutter, it’s important to consider the following factors:
1. Material Selection: Not all materials are suitable for CO2 laser cutting. Different materials have different properties that can affect the quality of the cut, such as thickness, density, and composition. It’s important to select materials that are compatible with CO2 laser cutting and to consider any special requirements for specific materials.
2. Focus and Beam Alignment: Proper focus and beam alignment are crucial for achieving a clean, precise cut. The laser beam must be precisely focused and aligned on the material to ensure optimal cutting performance. Regular maintenance and calibration of the laser cutting system are essential to maintain proper focus and alignment.
3. Cutting Parameters: Adjusting the cutting parameters, such as power, speed, and frequency, can have a significant impact on the quality of the cut. It’s important to experiment with different settings to find the optimal parameters for each material and thickness.
4. Assist Gas Control: The use of assist gas, such as nitrogen or oxygen, is essential for achieving a clean, burr-free cut. Proper control of the assist gas flow and pressure is crucial for achieving the best cut quality.
Common Troubleshooting Techniques
Despite careful optimization, issues may still arise during the CO2 laser cutting process. Some common troubleshooting techniques include:
1. Material Warping: If the material warps during cutting, it may indicate a problem with the assist gas flow or excessive heat buildup. Adjusting the assist gas flow and reducing the cutting speed can help alleviate this issue.
2. Rough Edges or Burrs: Rough edges or burrs can be caused by improper focus or assist gas control. Realigning the beam focus and adjusting the assist gas parameters can help improve edge quality.
3. Slag Formation: Slag, or residue buildup, can occur on the underside of the cut due to improper cutting parameters or assist gas control. Adjusting the cutting parameters and assist gas flow can help minimize slag formation.
FAQs
Q: How can I determine the optimal cutting parameters for a specific material?
A: Experiment with a range of power, speed, and frequency settings to find the optimal parameters for each material. Keep detailed records of the parameters used for different materials and thicknesses to guide future cutting processes.
Q: What maintenance practices are essential for ensuring consistent cut quality with a CO2 laser cutter?
A: Regular maintenance, including cleaning of optics, calibration of the laser system, and inspection of the assist gas delivery system, is essential for maintaining consistent cut quality.
Q: Are there any specific safety considerations for optimizing CO2 laser cut quality?
A: Safety is paramount when working with CO2 laser cutters. Proper training, use of personal protective equipment, and adherence to safety protocols are essential for optimizing CO2 laser cut quality.
In conclusion, optimizing CO2 laser cut quality requires careful attention to material selection, focus and beam alignment, cutting parameters, and assist gas control. By understanding the basics of CO2 laser cutting and implementing troubleshooting techniques, manufacturers can achieve the best possible cut quality with their CO2 laser cutter.